The Transformative World of Primer Printing
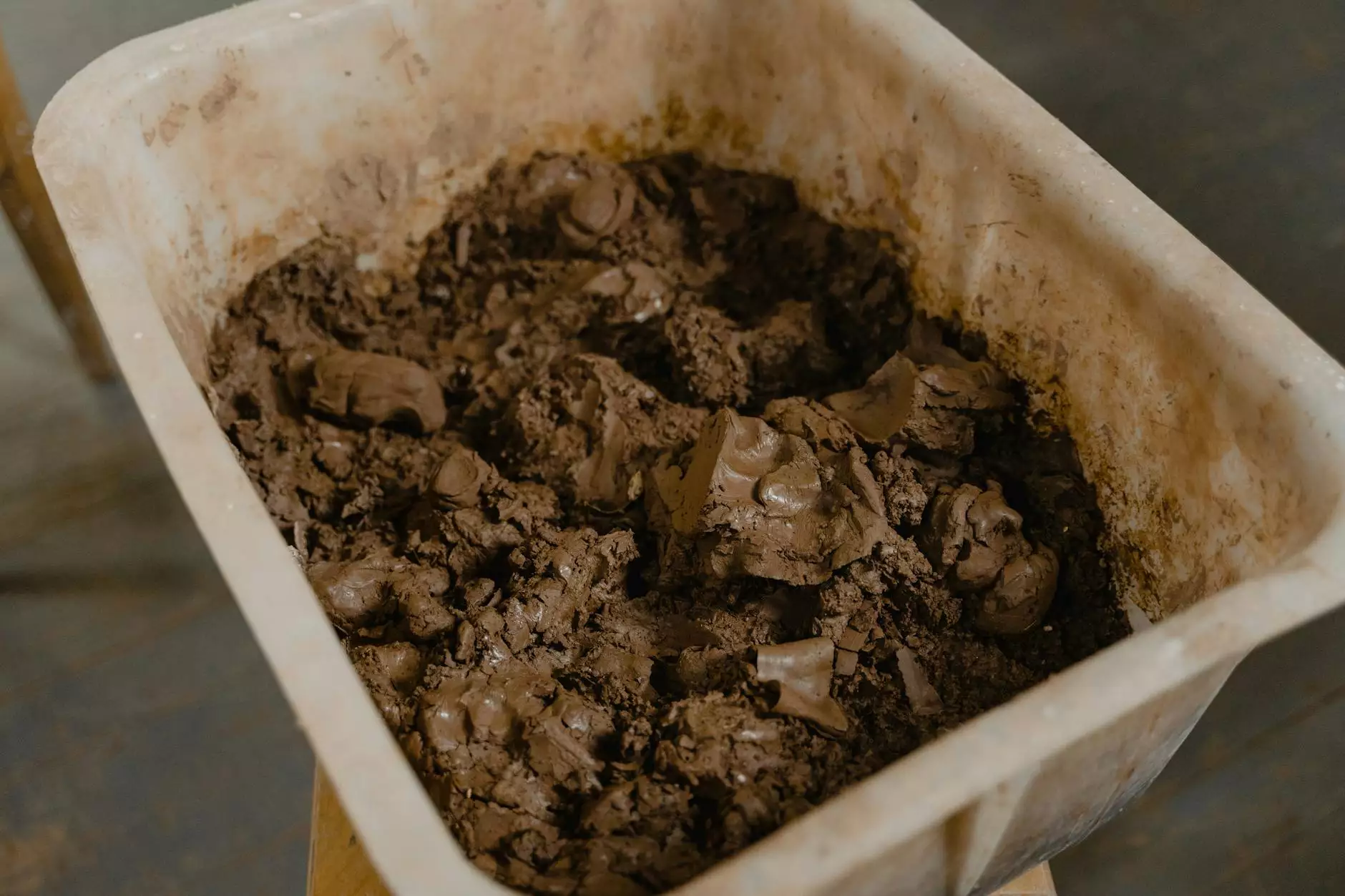
Primer printing is an essential aspect of modern business printing solutions that often goes overlooked. In a world where first impressions are critical, the quality and technique of printing can substantially impact your outreach and branding efforts. This article delves deep into what primer printing is, its advantages, and how businesses, including those in the printing services and electronics sectors, can leverage it for maximum benefit.
What is Primer Printing?
Primer printing refers to the application of a primer or base layer on surfaces before the actual printing process occurs. The primer primer layer serves several vital functions—it enhances the adhesion of inks, ensures a uniform print quality, and maximizes the vibrancy of colors. This process can be utilized across various materials, including paper, cardboard, metal, glass, and plastics, making it incredibly versatile.
Importance of Primer Printing in Today's Market
As businesses increasingly turn to high-quality printing as a means to convey professionalism, the role of primer printing has become more critical than ever. It influences not only the visual appeal of printed materials but also their longevity and durability.
Advantages of Primer Printing
The benefits of incorporating primer printing into your business processes are numerous. Here are some prominent advantages:
- Improved Ink Adhesion: When inks are applied over a properly primed surface, they adhere more effectively, reducing the risk of peeling and fading.
- Enhanced Color Vibrancy: Primming prepares the substrate, allowing for a more vibrant color display, which is crucial in brand representation.
- Increased Durability: The use of a primer helps to protect the printed material, making it more resistant to scratches, moisture, and other environmental factors.
- Better Coverage: A primer ensures that the ink covers the entire surface uniformly, eliminating blotchy prints and subpar aesthetics.
How Primer Printing Works
The efficacy of primer printing lies in its application. Here's a step-by-step process explaining how primer printing works:
Step 1: Surface Preparation
Before applying the primer, the surface must be cleaned and prepped to ensure optimum adhesion. This often involves removing any dust, oils, or contaminants that may interfere with the primer's ability to adhere.
Step 2: Primer Application
Once the surface is prepared, the primer is applied using various methods such as spraying, rolling, or brushing. The choice of application method typically depends on the surface type and the desired finish.
Step 3: Drying and Curing
After application, the primer must dry and cure appropriately. This is a crucial stage that determines the strength of the bond between the primer and the substrate.
Step 4: Printing
Once the primer is completely dry, the actual printing process begins. The well-primed surface allows inks to bed down effectively, resulting in print quality that surpasses unprimed surfaces.
Applications of Primer Printing
Primer printing is not limited to just one industry; its applications are wide-ranging. Here are some fields where primer printing is particularly beneficial:
1. Packaging Industry
In the packaging industry, primer printing is vital for ensuring that colors are vibrant and that the materials can withstand the rigors of transportation and handling.
2. Electronics and Product Branding
Electronic devices often require high-quality printing for branding. Using primer allows manufacturers to print directly onto surfaces like plastics and metals while maintaining clarity and longevity.
3. Signage and Displays
High-quality displays and signage benefit immensely from primer printing, which ensures that the graphic elements remain intact and bright, even in harsh outdoor conditions.
Choosing the Right Primer for Your Printing Needs
Understanding the specific requirements for your project is essential when selecting a primer. Consider the following factors:
1. Substrate Compatibility
Different materials require specific types of primers. Ensure that the primer you choose works well with the substrates you plan to print on.
2. Drying Time
The drying time of the primer can impact your overall project timeline. Select a primer that suits your production schedule while providing optimal performance.
3. Environmental Conditions
Consider the environment in which the printed materials will be used. For instance, outdoor signage requires primers that can withstand UV light and moisture.