Exploring the World of OEM Lathe Machining Parts Manufacturers
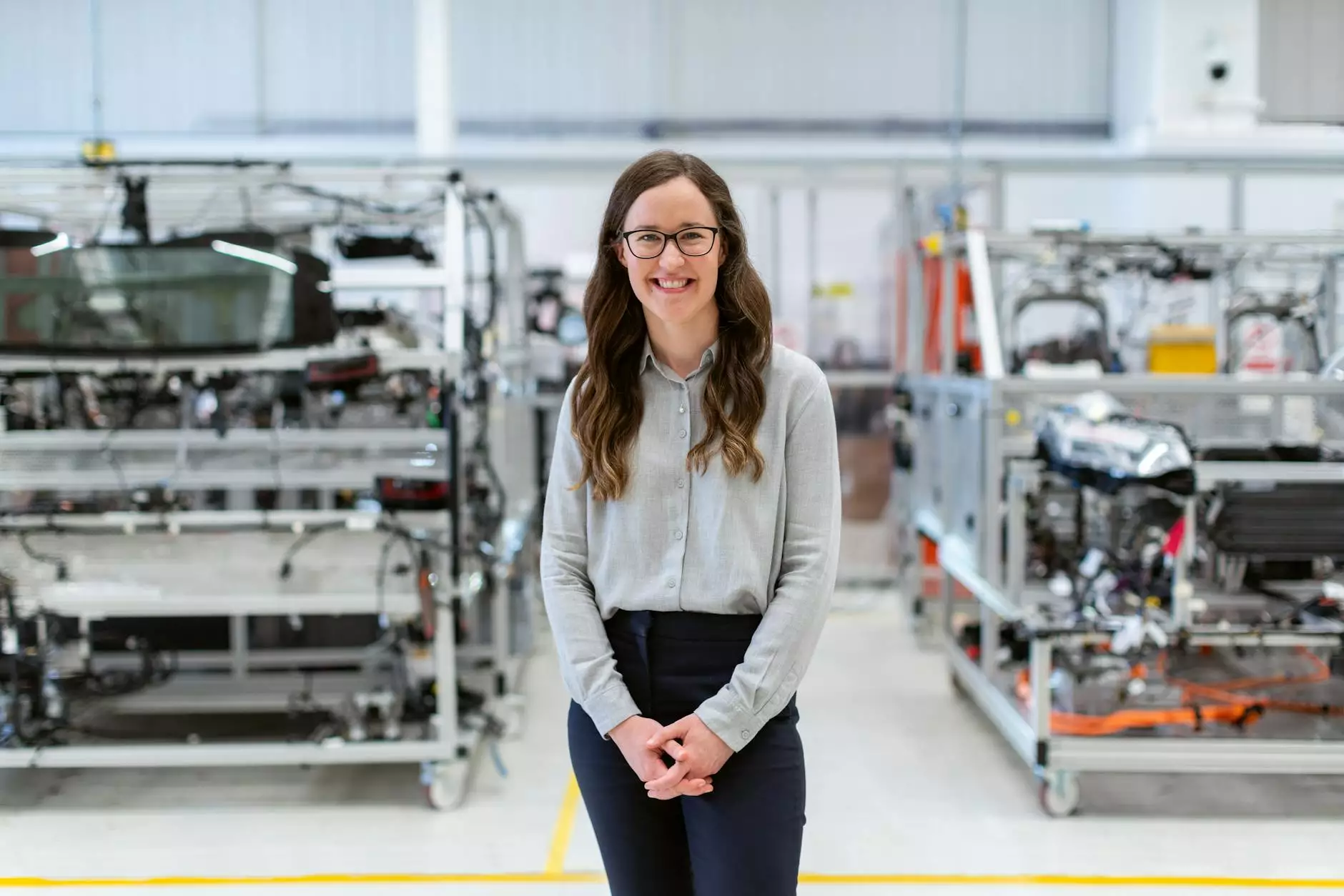
In the realm of manufacturing, the demand for precision and quality is paramount. This has given rise to a multitude of specialized suppliers and manufacturers, with OEM lathe machining parts manufacturers taking center stage. These companies play a critical role in various industries by providing high-quality, custom components that meet specific client requirements. In this article, we will delve into the intricacies of the OEM machining process, the benefits of working with these manufacturers, and the future trends shaping this essential sector.
The Role of OEM in Lathe Machining
Original Equipment Manufacturers (OEM) specialize in producing pieces that are integral to the assembly of larger systems. In the context of lathe machining, which involves the use of a lathe to remove material from a workpiece, OEMs focus on crafting components that require high levels of precision and accuracy.
- Customized Solutions: OEMs are adept at creating tailored components to fit the precise specifications required by various industries.
- Quality Assurance: Reputable OEM lathe machining parts manufacturers adhere to stringent quality standards, ensuring durability and performance.
- Innovation: Many OEMs invest in cutting-edge technology and practices to enhance their production process, leading to better quality products.
The Benefits of Working with OEM Lathe Machining Parts Manufacturers
Choosing to collaborate with OEM lathe machining parts manufacturers brings a multitude of advantages, particularly when it comes to quality, efficiency, and cost-effectiveness.
1. Superior Quality and Precision
One of the primary benefits of engaging with OEM manufacturers lies in their commitment to excellence. They utilize advanced machinery and techniques to achieve:
- High Tolerance Levels: OEMs can maintain exceptionally tight tolerances, which is crucial in ensuring components fit and work as intended.
- Consistency: With automated processes, manufacturers guarantee consistent quality across all produced parts.
- Material Expertise: OEMs often specialize in a range of materials, enabling them to select the best ones for specific applications.
2. Cost-Effectiveness
While the upfront cost of working with OEM manufacturers might be higher than sourcing cheaper alternatives, the long-term benefits drastically outweigh these costs. Consider:
- Reduced Waste: Precision machining minimizes material waste, making processes more economical.
- Lower Failure Rates: Higher quality means lower risk of product failures and recalls, ultimately saving costs.
- Longer Lifespan: High-quality components generally have a longer service life, reducing the frequency of replacements.
3. Increased Flexibility and Customization
OEM lathe machining parts manufacturers excel at providing customized solutions to meet unique customer needs. This capability includes:
- Tailored Designs: Engineers can collaborate with clients to develop specific designs that cater to their operational requirements.
- Rapid Prototyping: Many OEMs offer rapid prototyping services that allow companies to quickly test and refine their designs before mass production.
- Scalability: OEMs can scale production based on demand, allowing companies to adjust their operations without compromise.
Industries Benefiting from OEM Lathe Machining Parts
The applications of OEM lathe machining parts are extensive and varied, impacting numerous sectors, including:
Aerospace and Defense
The aerospace industry demands the highest standards of quality due to the critical nature of its products. Components must be meticulously engineered, crafted from lightweight materials, and undergo rigorous testing.
Automotive
In the automotive sector, OEM parts are vital for performance and safety. By sourcing parts from reputable manufacturers, companies can ensure their vehicles meet international standards.
Medical Equipment
The medical field relies on precision-engineered components to deliver life-saving devices. OEM manufacturers ensure that medical equipment is both safe and reliable through stringent quality checks and material selection.
Advanced Technologies in OEM Lathe Machining
As technology continues to evolve, so does the landscape of OEM lathe machining. Manufacturers are increasingly adopting advanced technologies to enhance their processes, which include:
1. Computer Numerical Control (CNC) Machining
CNC machining has revolutionized lathe manufacturing. By utilizing computer systems to control the machinery, manufacturers can achieve:
- Enhanced Accuracy: CNC machines can achieve far tighter tolerances than manual operation.
- Automation: Reduces labor costs and increases efficiency during the production process.
- Complex Designs: CNC machining allows for intricate designs that would be impossible or prohibitively expensive with manual machining methods.
2. Additive Manufacturing
3D printing is making its mark in the OEM space, offering:
- Rapid Prototyping: Manufacturers can quickly create prototypes for testing and approval.
- Material Versatility: A wider range of materials can be used in 3D printing than traditional methods permit.
- Customization: On-demand production allows OEMs to create parts tailored precisely to the client's specifications.
3. Real-time Data Analytics
With the integration of IoT (Internet of Things) technologies, manufacturers can track and improve their processes in real time, resulting in:
- Predictive Maintenance: Identifying and addressing issues before they lead to equipment failure.
- Performance Optimization: Continuous monitoring allows for constant improvements in operational efficiency.
The Future of OEM Lathe Machining Parts Manufacturing
The landscape of OEM lathe machining parts manufacturers is continually evolving, influenced by market demands and technological advancements. As we look to the future, several trends are emerging:
1. Sustainable Manufacturing Practices
The push for sustainability is leading OEMs to adopt greener manufacturing practices. By reducing waste and energy consumption, manufacturers can minimize their environmental footprint while meeting consumer demand for eco-friendly products.
2. Increased Focus on Automation
As technology progresses, the trends toward greater automation in manufacturing will likely continue. This shift promises to enhance productivity and quality while minimizing labor costs.
3. Greater Customization
As consumer needs evolve, the demand for highly customized solutions will grow. OEMs that can respond effectively to these needs will maintain a competitive edge in the industry.
Conclusion
In conclusion, OEM lathe machining parts manufacturers play an essential role in various industries, providing high-quality, precise components critical for the success of numerous applications. By embracing technology and innovation, these manufacturers are poised to meet the demands of the future, ensuring that they continue to provide solutions that meet and exceed industry standards. Collaboration with experienced OEMs can lead to enhanced product quality, reduced costs, and a significant competitive advantage in today's fast-paced market.
For more information about OEM lathe machining parts manufacturers and how they can benefit your business, visit deepmould.net today.